316 stainless steel plate is an austenitic stainless steel alloy known for its excellent corrosion resistance, particularly in chloride environments. It typically contains 16-18% chromium, 10-14% nickel, and 2.0-3.0% molybdenum, which enhances its resistance to pitting and crevice corrosion compared to 304 stainless steel. Due to its robust properties, 316 stainless steel plate is widely used in marine applications, chemical processing, and environments where high levels of corrosion resistance are required. Additionally, it maintains good mechanical properties at elevated temperatures.
Like 304 stainless steel, 316 stainless steel plate possesses excellent forming and welding characteristics. It can be easily formed or cut into various shapes for constructing a wide range of machinery.
Difference between 316 and 316L
The primary difference between 316 and 316L stainless steels lies in their carbon content and how this affects their properties:
Carbon Content:
- 316 stainless steel typically has a carbon content of up to 0.08%.
- 316L stainless steel has a lower carbon content, capped at 0.03%. This reduction in carbon enhances its corrosion resistance.
Corrosion Resistance:
- Both grades offer excellent resistance to corrosion, particularly in chloride environments. However, 316L's lower carbon content makes it slightly more resistant to corrosion, especially in welded areas where carbon could increase susceptibility to corrosion.
Welding and Fabrication:
- 316L is often preferred for welding applications because it minimizes the risk of carbide precipitation during the welding process, which can occur in higher carbon grades like 316. This makes 316L more suitable for projects that involve extensive welding.
Applications:
- Both grades are commonly used in marine environments, chemical processing, and food and medical applications. However, 316L is often favored in situations where lower carbon content provides critical advantages, such as in pharmaceutical or chemical processing equipment.
316/316L Stainless Steel Plate Applications:
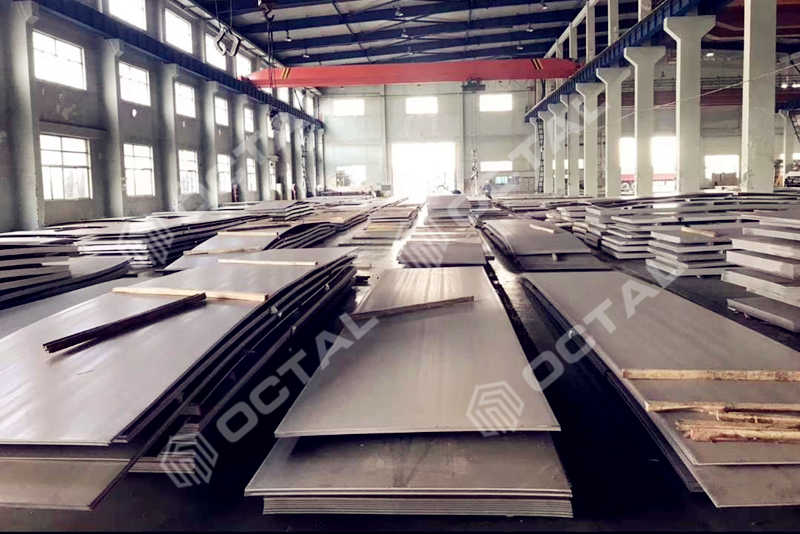
316 Stainless Steel Plate
Difference between 304 and 316 Stainless Steel
The main differences between 304 and 316 stainless steels relate to their chemical composition, properties, and applications:
Chemical Composition:
- 304 Stainless Steel: This grade typically contains 18% chromium and 8% nickel. It does not have molybdenum.
- 316 Stainless Steel: This grade contains 16% chromium, 10% nickel, and 2-3% molybdenum, which is added to enhance corrosion resistance.
Corrosion Resistance:
- 304: While 304 stainless steel offers good corrosion resistance in many environments, it is more susceptible to corrosion, particularly in chloride environments.
- 316: The addition of molybdenum in 316 improves its resistance to pitting and crevice corrosion, making it more suitable for marine and harsh environments.
Mechanical Properties:
- Both 304 and 316 exhibit similar mechanical properties, including strength and toughness. However, 316 typically performs better under chemical exposure due to its enhanced composition.
Applications:
- 304: Commonly used in kitchen equipment, food processing, and general structural applications.
- 316: Frequently used in marine applications, chemical processing, and medical devices due to its superior corrosion resistance.
316/316L Stainless Contains Mo Provides better Resistance to High Temperature
According to its chemical composition, 316 stainless steel contains molybdenum, which is why 316 and 316L exhibit better corrosion resistance than 304 and 304L, particularly in high-temperature conditions. As a result, engineers typically opt for 316 material in high-temperature environments. However, in environments that contain sulfuric acid, it is advisable not to use 316 or 316L at elevated temperatures, as molybdenum can react with sulfur ions, forming sulfides that may lead to corrosion.
321 Stainless Steel
321 stainless steel plate is an austenitic stainless steel alloy that contains titanium, typically in the range of 5 to 10 times the carbon content. This addition of titanium enhances its resistance to carbide precipitation during welding, making it particularly suitable for applications where exposure to high temperatures occurs.
316 Stainless Steel Chemical Composition (VS 304)
Elements (%) | 304 (S30400) | 304L (S30403) | 316 (S31600) | 316L (S31603) |
---|---|---|---|---|
Carbon, Max | 0.07 | 0.030 | 0.08 | 0.030 |
Manganese, Max | 2.00 | 2.00 | 2.00 | 2.00 |
Phosphorus, Max | 0.045 | 0.045 | 0.045 | 0.045 |
Sulphur, Max | 0.030 | 0.030 | 0.030 | 0.030 |
Silicon, Max | 0.75 | 0.75 | 0.75 | 0.75 |
Chromium | 17.5-19.5 | 17.5-19.5 | 16.0-18.0 | 16.0-18.0 |
Nickel | 8.0-10.5 | 8.0-12.0 | 10.0-14.0 | 10.0-14.0 |
Mo | ... | ... | 2.00-3.00 | 2.00-3.00 |
Nitrogen | 0.10 | 0.10 | 0.10 | ... |
316 vs 304 Mechanical Properties
Mechanical Properties | 304 (S30400) | 304L (S30403) | 316 (S31600) | 304L (S30403) |
---|---|---|---|---|
Tensile Strength Min | 75 Ksi [515 Mpa] | 70 Ksi [485 Mpa] | 75 Ksi [515 Mpa] | 70 Ksi [485 Mpa] |
Yield Strength Min 0.2% offset | 30 Ksi [205 Mpa] | 25 Ksi [170 Mpa] | 30 Ksi [205 Mpa] | 25 Ksi [170 Mpa] |
Yield Strength Min 1% offset | 36 Ksi [250 Mpa] | 35 Ksi [240 Mpa] | 38 Ksi [260 Mpa] | 38 Ksi [260 Mpa] |
Elongation Min | 40% | 40% | 40% | 40% |
Hardness Max | 92 HRB | 92 HRB | 95 HRB | 95 HRB |
Manufacturing Methods for 316/316L Stainless Steel Plate
The manufacturing methods for 316 and 316L stainless steel plates typically include several key processes designed to ensure the material's properties are preserved:
1. Melting and Alloying:
- The production begins with melting raw materials, including iron, chromium, nickel, and molybdenum, in a furnace. The mix is carefully controlled to maintain the desired chemical composition for 316/316L stainless steel.
2. Casting:
- After melting, the molten metal is cast into slabs or ingots. This can be done through processes like continuous casting or ingot casting. Continuous casting is often preferred for its efficiency and consistent quality of the resulting slabs.
3. Hot Rolling:
- The solidified slabs are then subjected to hot rolling, where they are heated to a specific temperature and passed through rollers to achieve the desired thickness. This process imparts strength and durability while enhancing the grain structure of the stainless steel.
4. Cold Rolling:
- For specific applications requiring finer tolerances and surface finishes, the hot-rolled plates can undergo cold rolling. This process is performed at room temperature and further refines the thickness and finish of the plates.
5. Annealing:
- Following the rolling processes, the stainless steel plates are often annealed. This heat treatment relieves internal stresses, improves ductility, and enhances corrosion resistance, particularly important for 316 and 316L grades.
6. Pickling and Passivation:
- After annealing, the plates may undergo pickling, which removes oxide scales, followed by passivation. Passivation enhances the chromium oxide layer on the surface, improving corrosion resistance.
7. Cutting and Finishing:
- Finally, the stainless steel plates are cut to the required dimensions and may undergo additional finishing processes, such as polishing, to achieve the desired surface quality.
Hot Rolling
Hot rolling for making the medium thickness plate from 4.5mm to 100mm.
Cold Rolling
Cold rolling for making a thin cold plate thickness of 0.02 to 4mm.
Heat Treatment
In order to ensure that the mechanical properties such as yield strength, tensile strength, elongation and hardness of all kinds of stainless steel plates meet the requirements, the steel plate must be subjected to heat treatment such as annealing, solution treatment and aging treatment before delivery.
316N, 316LN
After normalization, 316 or 316L becomes 316N or 316LN, respectively, resulting in improved yield strength of at least 320 MPa for thicknesses greater than 38 mm.
For thicknesses below 38 mm, the minimum yield strength for 316N is 550 MPa, with a tensile strength of 240 MPa. In comparison, 316LN has a minimum yield strength of 515 MPa and a tensile strength of 205 MPa.
Weight of 316 Stainless Steel Plate, Sheet, Coil
To calculate the weight of 314 stainless steel plate in kgs use the formula: length (m) x width (m) x thickness (mm) x 7.93
Our Supply Range
Standard: ASTM A240, ASME-SA240
Thickness Range: 0.02mm - 4mm, 4.5mm - 100mm.
Width Range: 900mm - 2400 mm
Length Range: 3000mm - 12000 mm, stainless steel coils
Surface Treatment: Natural, 2B, Mirror
Steel Cutting Services: Laser Cut Stainless Steel, Waterjet cutting , Plasma Cutting Services.